Sika Deutschland
Neues Intralogistik-Konzept für bessere Prozesse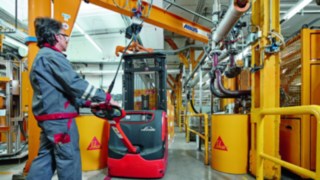
Passgenaue Materialflussprozesse bei einer in hohem Maße vereinheitlichten Stapler- und Lagertechnikgeräte-Flotte: Die Sika Deutschland GmbH, Tochterunternehmen des global tätigen Schweizer Konzerns und einer der weltweit führenden Anbieter von bauchemischen Produktsystemen sowie industriellen Kleb- und Dichtstoffen, erreicht dies mit einem logistischen Gesamtkonzept, das trotz kundenspezifischer Lösungen auf Vereinheitlichung setzt, sich auf eine Staplermarke konzentriert und die Geräte im Full-Service least.
Sika Deutschland gehört zu den Unternehmen, bei denen effizientes, nachhaltiges Wirtschaften einen hohen Stellenwert genießt. Aber auch die Optimierung der innerbetrieblichen Logistik ist stark in der Firmenphilosophie verankert. Ein Beispiel ist der Produktionsstandort Bad Urach am Rande der Schwäbischen Alb. Hier werden die größtenteils naturbasierten Grundstoffe in riesigen Behältern oder Fässern angeliefert und aufgrund des hohen Platzbedarfs möglichst zügig weiterverarbeitet. Was aus der Produktion kommt, wird direkt in unser Zentrallager nach Stuttgart-Weilimsdorf gebracht und dort kommissioniert, erzählt Michael Rath, Werksleiter am Standort Bad Urach. Ein Warenlager für Fertigprodukte gibt es in Bad Urach nicht. Durchschnittlich sieben Lkw docken pro Tag an den Verladerampen an, weitere Fahrzeuge werden im Hof beladen.
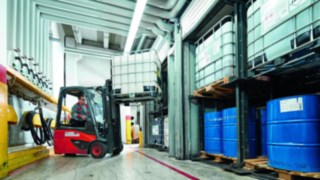
E-Stapler von Linde im Einsatz bei Sika Deutschland GmbH
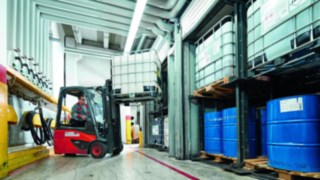
E-Stapler von Linde im Einsatz bei Sika Deutschland GmbH
In Bad Urach sind es vor allem die beengten Räumlichkeiten, die den Logistikverantwortlichen immer wieder zu schaffen machen. Enge Gassen und wenig Platz für Wendemanöver sind allgegenwärtig. Hinzu kommen eingeschränkte Deckentragfähigkeiten sowie niedrige Decken- und Durchfahrtshöhen. Die Fertigung unter dem Dach des historischen Gebäudes aus dem 19. Jahrhundert ist in zwei große Produktbereiche unterteilt: Ein- und Zweikomponenten-Kleb- und Dichtstoffe für diverse industrielle Anwendungen wie Gleiskörper, Windräder, Fensterabdichtungen oder Kühlcontainer auf der einen Seite sowie Hochleistungsharze, Platten und Pasten für den Modell- und Formenbau von Automobilen, Yachten oder Flugzeugen auf der anderen Seite. Eine weitere Besonderheit des Standortes Bad Urach ist die Lage im Herzen des Luftkurortes. „Aufgrund der Nähe zum Stadtzentrum verzichten wir komplett auf den Einsatz von verbrennungsmotorischen Staplern“, berichtet Rath. „Den hohen Umweltanforderungen entsprechen wir mit gesicherten Prozessen und lückenloser Überwachung.
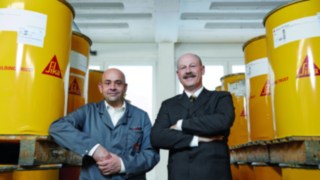
Michael Rath, Werksleiter am Standort Bad Urach und Atilla Böhm, Fuhrparkleiter
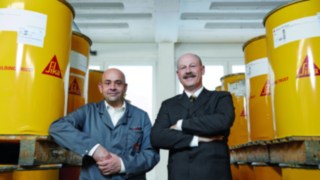
Michael Rath, Werksleiter am Standort Bad Urach und Atilla Böhm, Fuhrparkleiter
“ Zur Deckung seines Strombedarfs nutzt das Unternehmen bereits heute die Wasserkraft des durch das Werksgelände fließenden Flusses. „In Zukunft wollen wir diesen Anteil auf rund 40 bis 45 Prozent ausbauen“, erklärt der Werksleiter. Eine weitere Herausforderung ist das große Artikelsortiment. „Wir haben darauf ebenso wie auf schwankende Produktionsmengen mit einer entsprechenden Flexibilität unserer Prozesse zu reagieren“, weiß Rath. Bestimmte Produktionsbereiche unterliegen darüber hinaus der Ex-Schutzzone 1/21. Dort können sich bei Normalbetrieb gelegentlich Gemische aus Luft und brennbaren Gasen, Dämpfen oder Nebeln bzw. in der Luft enthaltenem, brennbaren Staub bilden. Flurförderzeuge, die dort zum Einsatz kommen, benötigen deshalb für alle sicherheitsrelevanten Komponenten eine EG-Baumusterprüfbescheinigung.
Neue Einkausstrategie
Vor rund vier Jahren beschloss das Unternehmen mit Hauptsitz in Stuttgart, ein Gesamtkonzept für die Intralogistik zu entwickeln. „Damit wollten wir erreichen, dass auch die Investitionen in Flurförderzeuge und Flottensoftware stärker auf die Effizienz unserer Fertigungsprozesse einzahlen“, formuliert Attila Böhm, Flottenmanager der Sika Deutschland GmbH, die Zielsetzung. In enger Zusammenarbeit mit Werksleitern und Materialflussverantwortlichen der insgesamt sieben Produktionswerke in Deutschland definierte der Flottenmanager am Ende der Konzeptphase drei wesentliche Vorgaben für die neue Einkaufsstrategie. Die erste Entscheidung lautete: weg vom Eigentum, hin zum Leasing mit Full-Service. Böhm begründet:
Ein Rentalvertrag schafft klare Zuständigkeiten und wir haben immer aktuelle Technik im Einsatz.
In enger Verbindung dazu stand der zweite Beschluss, sich auf eine Staplermarke - wenn möglich sogar standortübergreifend - festzulegen. „Für alle Themen rund um unsere Flurförderzeuge sollte es wenn möglich nur noch einen Ansprechpartner geben. Das hat erstens den Vorteil, dass immer die gleichen Servicetechniker vor Ort sind und sich perfekt auskennen. Folgen zweitens alle Geräte demselben Bedienkonzept, braucht niemand umzudenken. Das steigert die Produktivität und erhöht die Sicherheit im Betrieb. Und drittens beabsichtigten wir, uns über den Abschluss eines Rahmenvertrages bestmögliche Konditionen zu sichern“, sagt Böhm. Wenngleich er einräumt, dass diese Strategie für andere Unternehmen, beispielsweise aus der Automobilindustrie, wohl nicht in Frage käme. Denn dort gehe man den bisher auch bei Sika Deutschland praktizierten Weg, die Zusammenarbeit auf eine breite Basis zu stellen und mit mehreren Flurförderzeug-Herstellern zusammen zu arbeiten. „Ganz bewusst haben wir uns aber für die andere Variante entschieden, um unsere Prozesse zu optimieren“, erklärt Böhm. Der dritte Teil der neuen Einkaufstrategie galt der Reduktion der Modellvielfalt. „Statt Geräte mit unterschiedlichen Tragfähigkeiten haben wir jetzt beispielsweise nur noch das jeweils größere Modell im Einsatz und sind flexibel.“
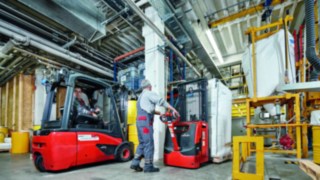
Hohe Anforderungen an die Logistik
Dass die Entscheidung auf Linde Material Handling als Generalausstatter fiel, ist nach Aussage von Werksleiter Michael Rath sowohl auf das engmaschige Service-Netz der Linde-Vertriebspartner unter Leithändlerschaft von Schöler Fördertechnik zurückzuführen, als auch auf die einfache Handhabung der Linde-Geräte.
„Für uns war klar, dass wir unsere Mitarbeiter in den Auswahlprozess einbeziehen. Dabei sollten aber nicht Bauchgefühl oder liebgewonnene Gewohnheiten die Grundlage der Entscheidung bilden, sondern sachliche Kriterien und Fakten. Deshalb haben wir beispielsweise unsere Staplerfahrer Bewertungsbögen ausfüllen lassen und die Geräte verschiedener Hersteller intensiven Vergleichstests unterzogen“, schildert Rath das Vorgehen.
Das Ergebnis am Ende war eindeutig: alle Werke haben sich mehrheitlich für Linde entschieden.
Mittlerweile wurde die Flotte Schritt für Schritt erneuert. Bei dem vorerst letzten Gerät handelt es sich um einen ex-geschützten Hochhubwagen mit gekürzter Radbasis und speziellem Anbaugerät zum Greifen und Kippen von offenen oder geschlossenen Fässern. Wenn dieser sog. Fasskipper für den ex-geschützten Bereich in ein paar Wochen geliefert ist, hat das Projekt seinen vorläufigen Abschluss gefunden.
„Trotz der Einsparung von sechs Geräten haben wir zahlreiche Optimierungen in den Abläufen unserer Werkslogistik erzielt“, resümiert Werksleiter Rath. Dafür gesorgt hat nicht zuletzt das gegenüber früher deutlich vergrößerte Spektrum an Ausstattungs- und Anbauvarianten sowie kundenspezifischen Lösungen. Rund zwei Drittel der insgesamt 30 im Werk eingesetzten Stapler und Lagertechnikgeräte sind auf die besonderen Gegebenheiten angepasst.
Für den Transport der zahlreichen überdimensionalen Warenträger und Behälter wurden zum Beispiel einige Stapler und Niederhubwagen mit überlangen Gabelzinken ausgestattet. Eine weitere materialflussplanerische Neuerung, die mit dem Austausch der Flurförderzeug-Flotte seit 2013 Einzug gehalten hat ist, dass Fässer, Behälter und Paletten in ein und demselben Arbeitsschritt gewogen und zum jeweiligen Bestimmungsort befördert werden.
Eine kontinuierliche Verbesserung unserer Prozesse ist uns sehr wichtig.
Michael Rath, Werksleiter bei Sika am Standort Bad Urach
Vorausschauende Wartung rückt in den Mittelpunkt
Reichlich Potenzial wird es mit dem bevorstehenden „Go-Live“ des Linde-Flottenmanagement-Lösung „connect:“ geben. „Die technischen Systemvoraussetzungen im Werk haben wir bereits geschaffen“, schildert Werksleiter Rath. Insbesondere von Funktionalitäten wie Zugangssteuerung, Schocksensorik und Nutzungsanalysen versprechen sich die Materialflussverantwortlichen eine weitere Optimierung der Prozesse und mehr Sicherheit im Betrieb.
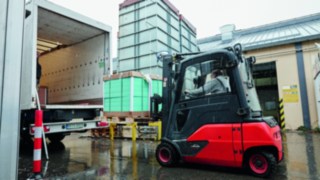
E-Stapler von Linde beim Beladen auf dem Betriebsgelände von Sika
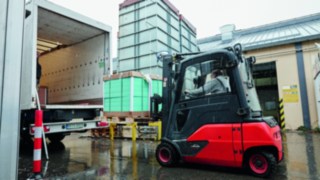
E-Stapler von Linde beim Beladen auf dem Betriebsgelände von Sika
Die Datenübertragung von Stapler zu Firmennetzwerk erfolgt über W-LAN. „In Zukunft würden wir diese Datenvernetzung gerne auch für eine vorausschauende Wartung nutzen“, plant Flottenmanager Böhm. „Im Idealfall sendet das Gerät Fehlermeldungen direkt zu unserem Servicepartner. Wenn dann der Service-Techniker von Schöler ins Werk kommt, hat er bereits das passende Ersatzteil mit im Gepäck.“ Damit wäre das Werk in Bad Urach erneut Pilot-Standort einer innovativen Lösung zur Prozessverbesserung.
Über Sika Deutschland GmbH
Als Tochterunternehmen der global tätigen Sika AG, Baar/Schweiz, zählt die Sika Deutschland GmbH mit über 1.100 Mitarbeitern und rund 545 Millionen Euro Jahresumsatz zu den weltweit führenden Anbietern von bauchemischen Produktsystemen und industriellen Dicht- und Klebstoffen. Für den Klebstoff Sikaflex Ultra-High Modulus, der am Standort Bad Urach gefertigt wird, erhielt Sika den Premier Automotive Suppliers’ Contribution to Excellence (PACE) Award 2015. Der schnell aushärtende Klebstoff kommt unter anderem beim BMW i3 und i8 zum Verkleben des Life-Moduls, der Fahrgastzelle aus kohlefaserverstärktem Kunststoff, und dem Drive-Modul, dem Chassis aus Aluminium, zum Einsatz